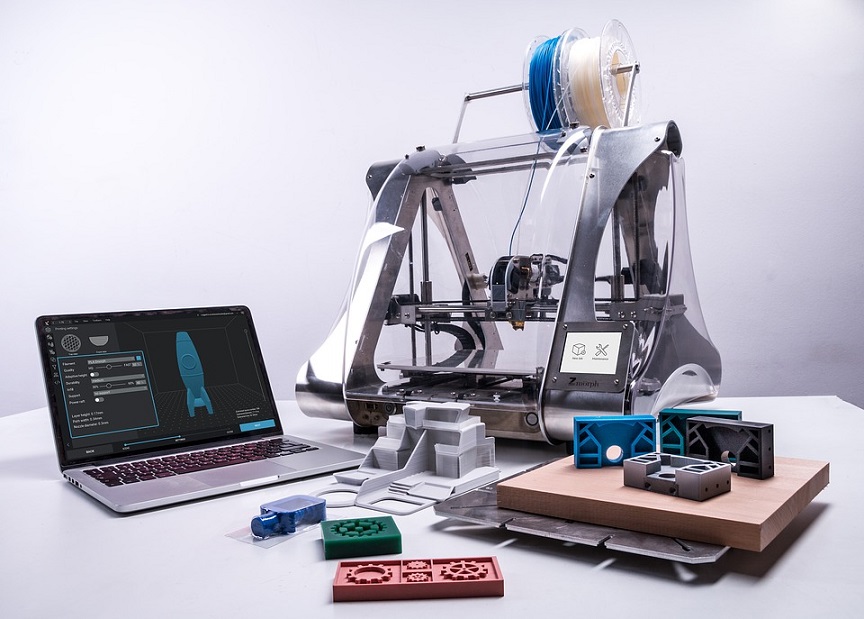
Pass or Fail: 3D Printed Concrete Homes
3D printing has become a trend in recent years; everyone seems to be aware of the technology in some way, whether they saw it on TV or read about it online. There is tons of hype over the ability to manufacture one solid piece of material onsite, supposedly leading to the decentralization of manufacturing. However, much of this hype is due to a widespread misunderstanding of the technology and its limitations. Many people have seen promotional videos and articles sporting titles like “3D Printed Concrete Home for Only $10,000” and “3D Printed Concrete Home Able to Withstand 8.0 Earthquakes”, but all of these pieces of content only ever show one side of the picture. Yes, 3D printing could be hugely effective in homing people when natural disaster strikes, but in terms of using the technology for your next new build, the technology falls short in many ways.
3D Printed Homes Do Not Use Reinforced Concrete
Concrete has extraordinary compressive strength, but weak tensile strength. Simply put, it is very difficult to crush concrete, but much easier to pull it apart. Embedding steel bars (AKA rebar) into the concrete creates “Reinforced Concrete”- ultimately making the concrete tougher to pull apart. Without rebar to reinforce the concrete, concrete is not a suitable material for Bay Area home building.
Incorporation of Remaining Trades is Difficult
Having a home made entirely out of concrete poses a huge issue: How do you finish out the rest of the trades? Nailing to concrete is no easy task. How does one go about turning what begins as a bunker, into a home? Concrete Shells has a non-structural wood interior that covers this issue, but 3D printed homes cannot easily complete the remaining trades.
Creates a “Lego Wall” Structure
3D printing uses a layer by layer manufacturing technique. This is their greatest attribute but also their largest issue. The layers mean that the structure has laminate weaknesses (AKA the layers do not stick together as well on the vertical axis as they do on the horizontal axis). This creates a “Lego Wall” situation, where the structure feels strong when you press down on it, but weak and fragile when you push the wall from the side.
Work Hours Limitation Creates Cold Joints
Many companies with 3D printing technology boast extremely rapid completion times such as “3D Printed Concrete Home Manufactured in 24 Hours”. This would be really cool, except for the United States has several laws that ban construction work at night. Thus, the 3D printing machine could only run for a set amount of hours during the day. Since you would not be able to work all 24 hours straight through, your structure’s concrete would have cold joints. Using basic terms, the concrete hardened to much before all of the concrete was able to be poured.
Site Preparation
We can 100% guarantee you that the companies advertising “3D Printed Concrete Home for Only $10,000” did not include excavation and foundation work. A huge expense in putting up any new structure is preparing the site for the new structure. The foundation is what ultimately determines the strength of a structure; because a Concrete Shells monolithically casts the foundation with the entire home, the site preparation goes hand in hand and is included in the price.
Our Consensus:
Based on the above information, Concrete Shells has no choice but to FAIL 3D Printed Concrete Homes. We absolutely love the idea of manufacturing a home on site and being able to quickly provide shelter to those in need during hard times, but all of these downsides make this technology impractical for Bay Area residential building.